The shortage of skilled welding specialists has been a longstanding challenge in the manufacturing and construction industries. According to a study by the European Labour Authority (2022), welding specialists ranked 3rd most lacking specialists in the EU. The shortage is particularly acute in countries like Germany, where there is a growing demand for skilled welders in the automotive and manufacturing industries.
This problem has led to delays, increased costs, and compromised project quality. However, the advent of laser welding technology has brought a ray of hope to address this shortage by offering numerous benefits that make it a viable solution. In this article, we’ll explore how laser welding technology can help solve the problem of the welding specialist shortage.
Automation and Simplified Operation 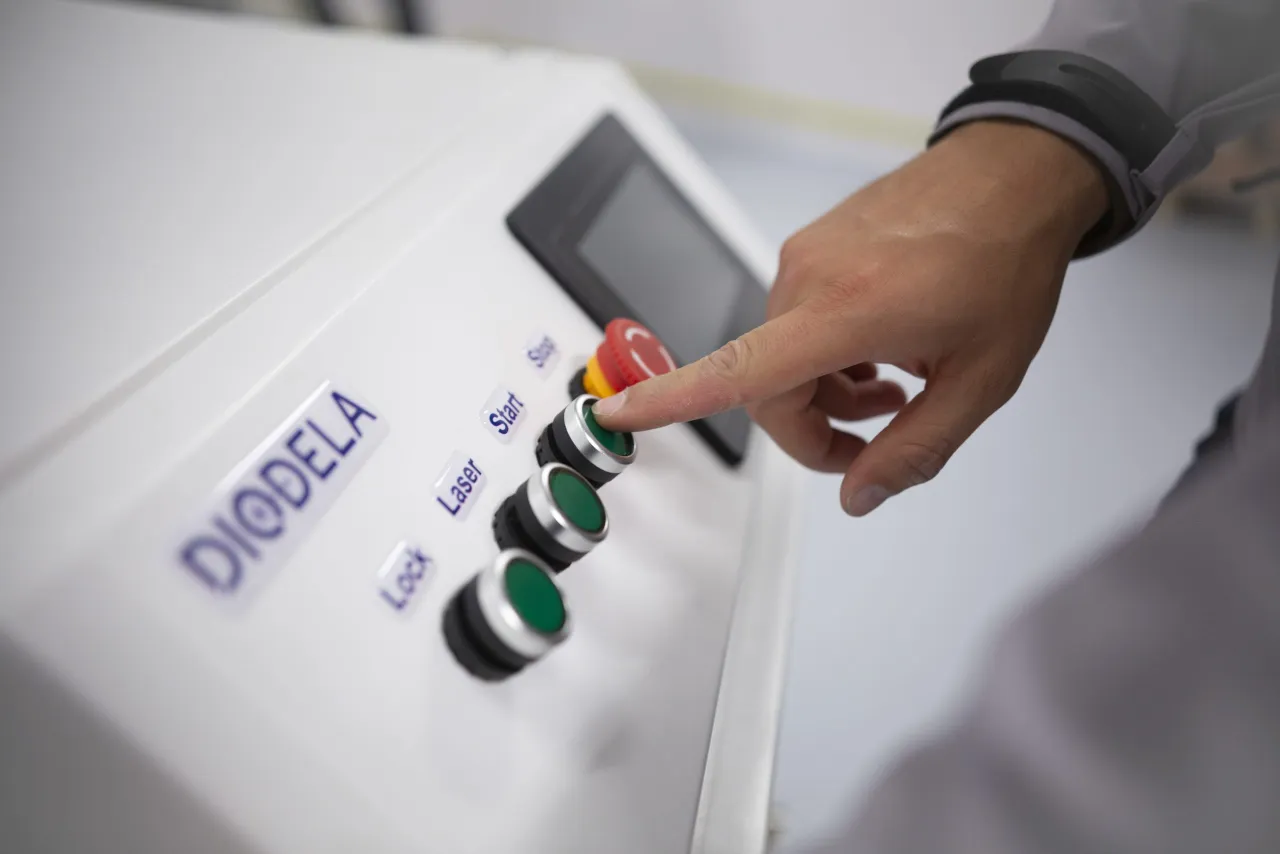
One of the key advantages of laser welding technology is its high level of automation and simplified operation. Unlike traditional welding methods that require extensive training and expertise, laser welding systems can be operated by individuals with basic technical skills. This means that a broader range of workers can be trained to use laser welding machines, reducing the reliance on a limited pool of highly skilled specialists.
In addition, laser welding can be easily integrated with a robotic arm. See our video here
Speed and Efficiency
Laser welding technology is known for its speed and efficiency. The precision and speed at which laser beams join materials are unmatched by traditional welding methods. This translates to shorter project timelines and increased productivity. As a result, even with a shortage of welding specialists, manufacturing and construction projects can continue at a steady pace. To put this in numbers, 1 laser welding system can replace 5 MIG or 10 TIG machines by its speed.
Consistency and Quality
Laser welding offers consistent, high-quality results, as the process is highly controlled and repeatable. The precision of laser beams reduces the likelihood of defects, such as porosity or weak welds. This means that projects can be completed with a higher level of quality assurance, reducing the need for extensive rework or costly repairs.
Reduced Safety Risks
Traditional welding methods involve safety hazards like arc flash, toxic fumes, and physical strain. Laser welding, on the other hand, eliminates many of these risks. It reduces the need for personal protective equipment and minimizes exposure to hazardous fumes. This makes welding more accessible to a wider range of workers, including those who might be deterred by the safety risks associated with traditional methods.
Cost Efficiency
Laser welding technology, while requiring an initial investment in equipment, can lead to significant cost savings in the long run. The reduced need for highly skilled welders and the increased speed of welding operations contribute to lower labor costs. Additionally, the higher quality and consistency of laser welds result in fewer post-welding inspections and repairs, further reducing project expenses.
Conclusion
The shortage of welding specialists has long been a concern for the manufacturing and construction industries. However, laser welding technology is emerging as a promising solution to this problem. By offering automation, speed, consistency, reduced safety risks, and cost-efficiency, laser welding technology can bridge the gap created by the welding specialist shortage. As industries continue to adapt to this innovative welding method, the need for highly specialized welders will diminish, making it easier to maintain project schedules, ensure quality, and reduce costs, all while addressing the labor shortage.
Choosing the right laser welding system
We are ready to help you choose the most effective laser welding system for your business needs. Contact us for individual consultation sales@diodela.lt
Diodela is a Photonics solutions provider for Industry based in Lithuania (EU). Using FTMC developed and exclusively licensed laser technology our company produces Industrial laser systems for laser welding, cleaning, and other photonics-based material processing. Due to close collaboration with laser science centers and vast experience in photonics, Diodela team is able to build innovative and precise laser systems that meet all Industrial needs.
Sources:
European Labour Authority (2022) https://www.ela.europa.eu/sites/default/files/2023-03/eures-labour-shortages-report-2022.pdf