Industry Practices
Laser Welding Applications
Laser welding is a versatile and efficient process applicable to a wide range of materials. Its precision and ability to produce strong, clean welds make it ideal for various industries. By leveraging laser welding, manufacturers can achieve high-quality results with minimal thermal distortion and excellent repeatability.
Automotive
Welding numerous automotive components such as airbag initiators, batteries, and fuel injectors, ensuring high-strength welds.
Aviation
Welding different metals with precision, avoiding material damage due to precise heat input, and achieving high-strength welds. Mostly used to weld engine components, panels and structural components.
Electronics
Utilized in the production of electronic components for devices like LEDs and consumer electronics such as mobile phones or TVs, enabling the creation of precise and intricate joints.
Medical
Essential for fabricating medical devices such as surgical instruments, implantable devices, and diagnostic equipment, ensuring hermetic seals, precision, and biocompatibility.
Semiconductors
Laser welding is used for joining micro-sized semiconductor components, such as integrated circuits and microchips, ensuring precision, reliability, and electrical conductivity.
Furniture Manufacturing
Facilitates precise welding of aluminum and steel components. Its capability to store ensures consistent results and saves preparation time.
Suitable Materials
Metals
Materials like copper and brass can be laser welded, though their high reflectivity and thermal conductivity require advanced techniques. These are commonly used in electrical components, plumbing fittings, and heat exchangers.
Non-ferrous Metals
Materials like copper and brass can be laser welded, though their high reflectivity and thermal conductivity require advanced techniques. These are commonly used in electrical components, plumbing fittings, and heat exchangers.
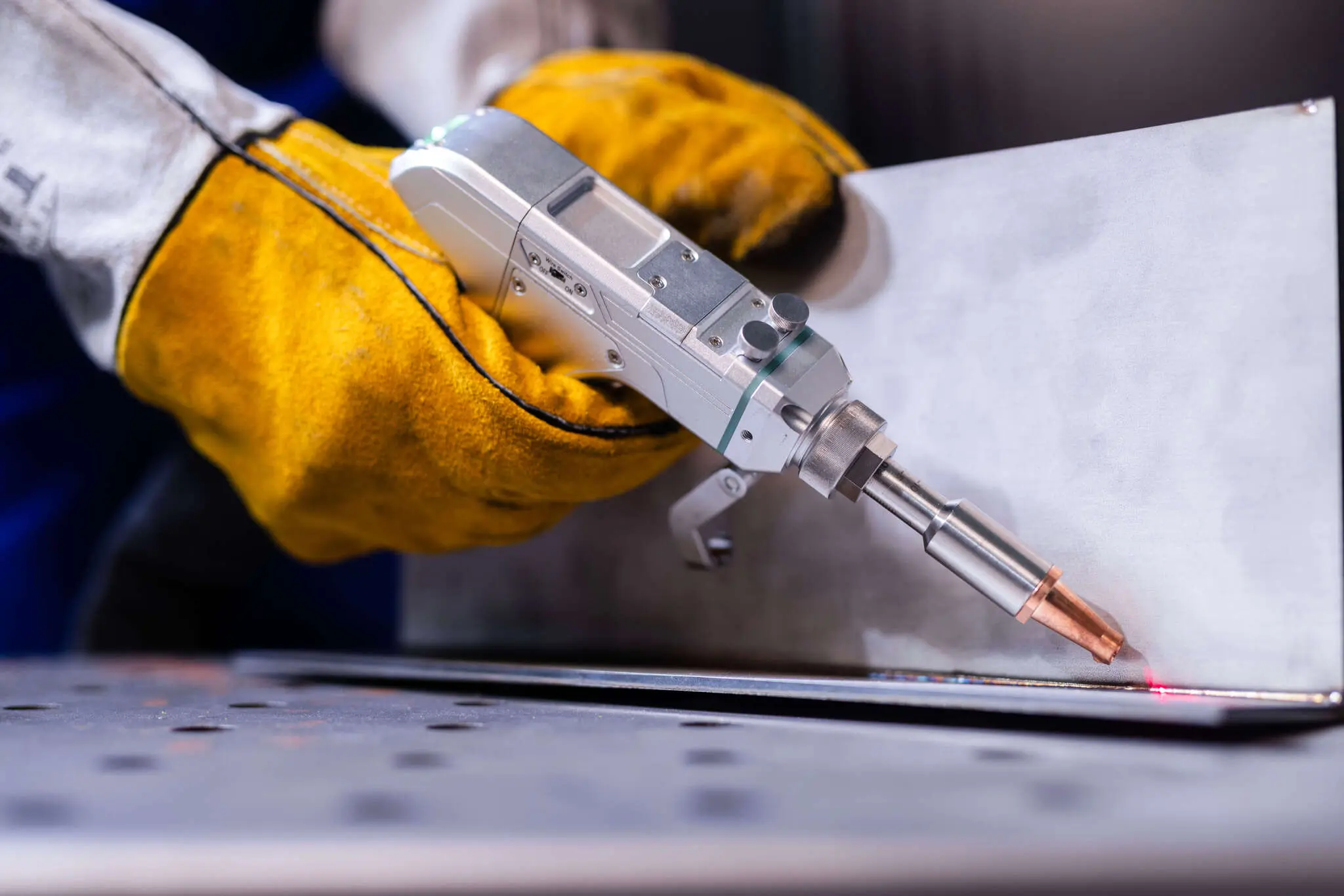
Plastics
Thermoplastics (acrylic, polycarbonate, polyethylene) and composite plastics can be laser welded. This method is widely used in packaging, automotive interiors, and consumer electronics for creating strong, lightweight joints.
Dissimilar Materials
Laser welding can join different metals (e.g., stainless steel to carbon steel) and metals to plastics, creating versatile, hybrid joints. These are crucial in applications requiring a combination of lightweight and structural integrity.
Unlimited Possibilities
Laser Welding Application Gallery
Technology Features
Laser welding is a revolutionary welding method that surpasses conventional techniques in efficiency and quality.
High Efficiency
Laser welding is 5 times faster than MIG and 10 times faster than TIG welding methods. Handheld laser welding speed is 1-5 m/min., while robotic laser welding speed is up to 12 m/min.
Minimal Physical Distortion
Laser welding effectively avoids thermal and physical distortion, particularly beneficial when joining thin large sheets, resulting in a pristine end product without the need for additional processing.
Low Welding Oxidation
By providing precise heat input to the desired area, laser welding ensures narrow full penetration welds, resulting in aesthetically pleasing final results with minimal welding oxidation.
High-Strength Welds
Laser welding produces welds that boast both consistency and high strength. Laser welds can be monolithic without filler metal when the distance between materials to be welded is up to 100 um.
Excellent Mechanical Properties
Laser welding preserves the material’s structural properties, ensuring that the welded components retain their original mechanical characteristics.
Ultimate Precision
Laser welding offers unparalleled accuracy, even for users without a welding background, due to the absence of laser light reflection, easy manipulation, and precise heat input to the targeted area.
How Does It Work
Laser beam welding is an advanced industrial process employed to seamlessly join various materials, forming robust and enduring welds. By focusing a high-intensity beam of light onto the desired welding area, this method effectively melts the materials together, creating a strong and permanent bond.